In this competitive world, in the long run, only the best can survive in the market. To become the best, it is quite essential to develop and market products that are of world-class quality. To attain these high standards it is essential that we imbibe a spirit of "Quality Consciousness" among the people who work for the organization. To develop Quality consciousness, a study of the Quality circle will be of great help since it covers various aspects regarding the achievement of desired quality as regards products and services, Professor Ishikawa Propounded the theory of "Quality Circle theory". In fact, the actual concept and design were given a concrete shape by methodical and scientific study after making observations in corporate Giants like SONY, MITSUBISHI ELECTRIC & TOYOTA, The word Quality circle signifies that a small group of people who are engaged in similar work within the organization who meet on regular basis under the leadership of Team supervisor to identify and discuss the problems in "Work areas" and sort out the problem in "Work areas" by taking necessary actions and to implement the remedies affecting the "Work areas" in specific and the "organization" as a whole.
The actual implementation of the Quality circle is done after making a systematic review of the organization. The Quality circle differs from a "Flat organization" vis a vis "Hierarchical Organization" There can be any number of Quality circles within an organization depending upon the size and nature of the activity of the organization. Each circle may consist of one leader and about 5 subordinates drawn from various departments. The leader should have hands-down experience in the actual work area. He should be knowledgeable and technically competent to clear off any doubts that the subordinates may pose to him. The leader looks after the training of his subordinates, leads the group discussions and jots down the suggestions made by the subordinates. The subordinates are given training in Quality control techniques and other related tools Quality control. The subordinates are exposed to new sets of Ideas, separating a problem into vital few and trivial many elements.
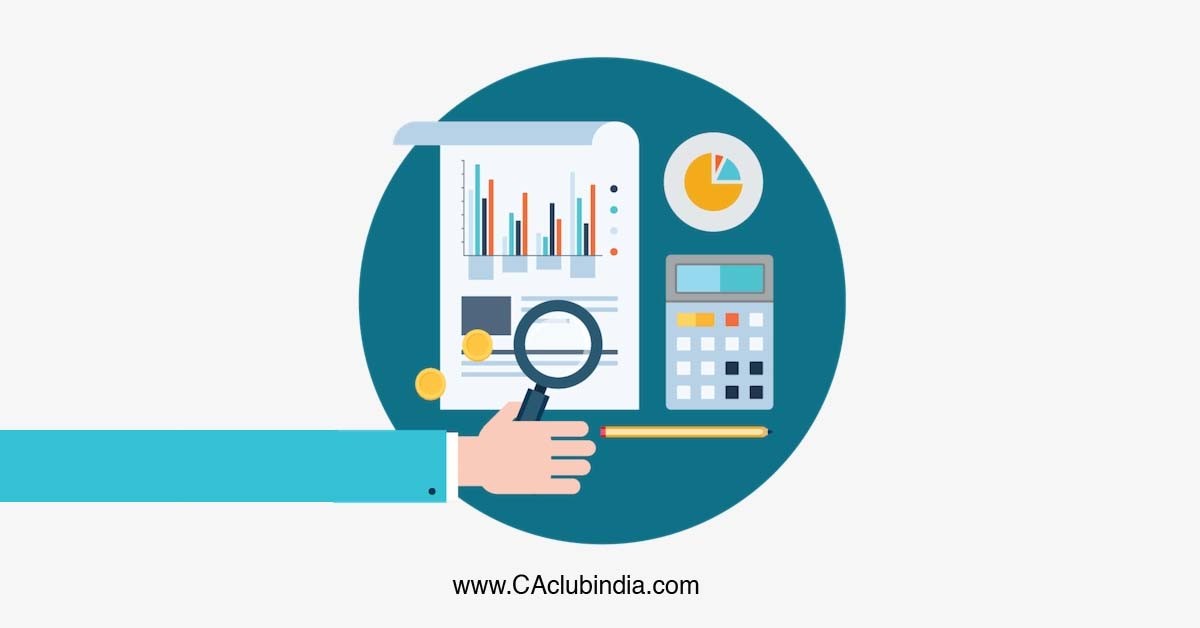
The actual working of a Quality circle is facilitated by the meeting of the leader and his subordinates. The day-to-day problems experienced by the subordinates within the organization like production bottlenecks distribution bottlenecks, breakdown of machinery, and unforeseen calamities are brought into the picture. As a first step in the implementation of the Quality circle, a blueprint of the case study is prepared and the remedies are listed for the prevention of the problem. The second step begins with members putting forth their views on different facets of the problem through Group discussion. This helps unlock the creative power of the group. The third step is entirely devoted to data collection and in-depth analysis, figures are drawn by using Histograms, Bar diagrams, and Pie charts, to project the Magnitude of each problem. The last step dedicates itself entirely to taking effective decisions and enables the team to prioritize decisions for effective implementation Before embarking upon implementing the Quality circle there are certain requirements to be followed by the organization desiring to Implement the Quality circle program.
They are as follows:
1) Awareness
For any program to be successful, full cooperation from the employees is essential in order to extract their cooperation, there should be awareness among the employees about the Quality circle program.
2) Management Participation
For the Quality circle to be successful active participation of top and middle management in the Quality circle program is an important precondition for the success of the program.
3) Work Experience
The employees selected as members of Quality circles must have adequate Qualifications and Experience in the field of work so as to enable them to discuss matters freely and to make constructive suggestions. The attitude of Managers, supervisors, and employees must be helpful toward changes in the working styles. A climate of understanding and a spirit of cooperation between Management and employees is essential.
Quality Circles differ from the conventional techniques of human resource development. It works from a bottom-up approach drawing directly on the knowledge and skill at the shop floor as against a top-down approach. Since the system of quality circles is based upon the mutual participation of both Management and workers, several tangible and intangible benefits follow. Some of the tangible benefits include an increase in production and productivity, improvement in the quality of products, higher efficiency, and reduced costs on a permanent basis. The intangible benefits include enhancement of morale and motivation levels of employees flowering of latent potential, their willingness to take higher responsibilities, improvement in communication between departments, development of team spirit, and an increased sense of participation in the organization.